How 3D metal printing change the world?
This chapter is for those who are interested in 3D printing in metal and the most interesting uses of metal printing in the world today,
In addition, the chapter will cover amazing success stories in metal printing and the innovative options that 3D printing in metal allows.
The factories of the future, the fourth industrial revolution
In the 18th and 19th centuries a revolution took place. This revolution enabled humanity to open new doors to progress and technological development that changed the world, it was of course the Industrial Revolution. One of the factors that enabled the existence of the Industrial Revolution was the establishment of factories. While factories have been major players in the Industrial Revolution and have served and are still serving humanity to this day, factories have significant shortcomings that are increasingly felt as humanity moves forward.
In the 21st century everything is constantly changing, new ideas for products and technologies are evolving every day. Factories find it difficult to meet rapidly changing dynamic needs. In order to produce a new product, a factory usually has to be equipped with a new machine – a process that delays the development and creation of innovative products.
This is why in the 21st century we are on the brink of the fourth industrial revolution that will provide a solution to the rapidly changing needs of humanity. The forerunners of the revolution are 3D printers. It is likely that the plants of the future will be based mainly on 3D printing technology – metal printers and plastic printers.
Metal printing has huge potential to enable future factories to quickly produce different products in one machine. 3D printing in metal allows not only production flexibility but also the creation of complex geometric structures that cannot be created by any traditional method, along with saving raw material, money and manpower.
Whereas in its infancy, metal printing technology was the most expensive, nowadays metal printing prices are constantly falling. Today metal printing competes directly with traditional production methods, and in some products it pays significantly more in terms of production capabilities, cost and utilization of the material.
In this chapter we will review the most revolutionary uses of metal printing in the various industries, enabling the creation of products that were not previously manufactured at all.
3D metal printing is making a global change
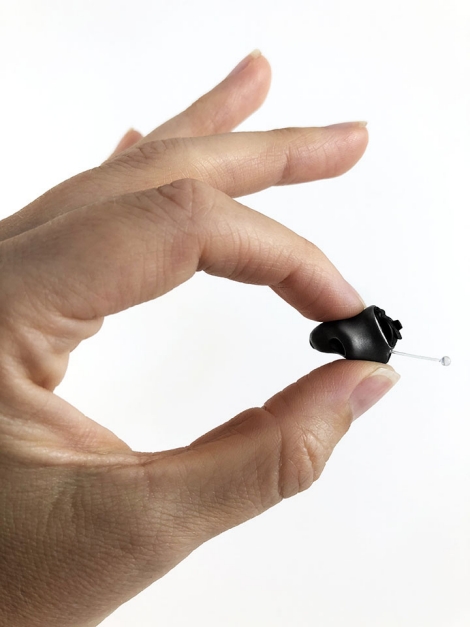
Phonak, one of the world’s leading companies in the field of hearing aids, launched the Virto B-Titanium hearing aid in 2017. The Virto B is a tiny hearing aid that is made using 3D metal printing. The printing of the device in metal allowed the creation of an extremely thin wall with a thickness of only 0.2 mm! Thin thickness at 50% more than previous tiny hearing aids from the Phonak company and 15 times stronger than standard acrylic envelopes.The combination of the metallic raw material and the innovative capabilities enabled by 3D printing technology, opened a door to create a revolutionary-discreet hearing aid, small in size, lightweight and ideal for maximizing hearing quality. Virto B is the smallest hearing aid that Phonak has ever produced in the field of personalization! Its tiny size was made possible by the metal printing, which allowed the creation of a thin but durable and strong shell for the hearing aid.
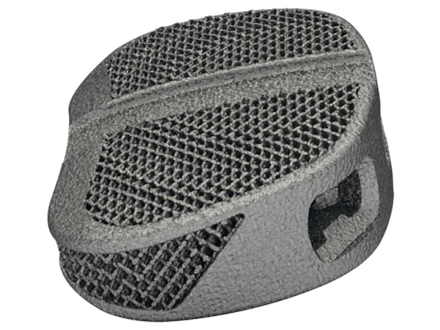
Printed implants for spinal injuries mimic the natural bone structure
EIT (Emerging Implant Technologies company, which specializes in manufacturing implants and medical devices for spinal problems, has created innovative implants using 3D metal printing. Implant printing In a metal printer, allowed EIT to simulate the natural bone structure of the printed product. Enables the creation of complex geometries that cannot be manufactured using traditional technologies. The parts are lightweight and customized for each patient according to his needs.
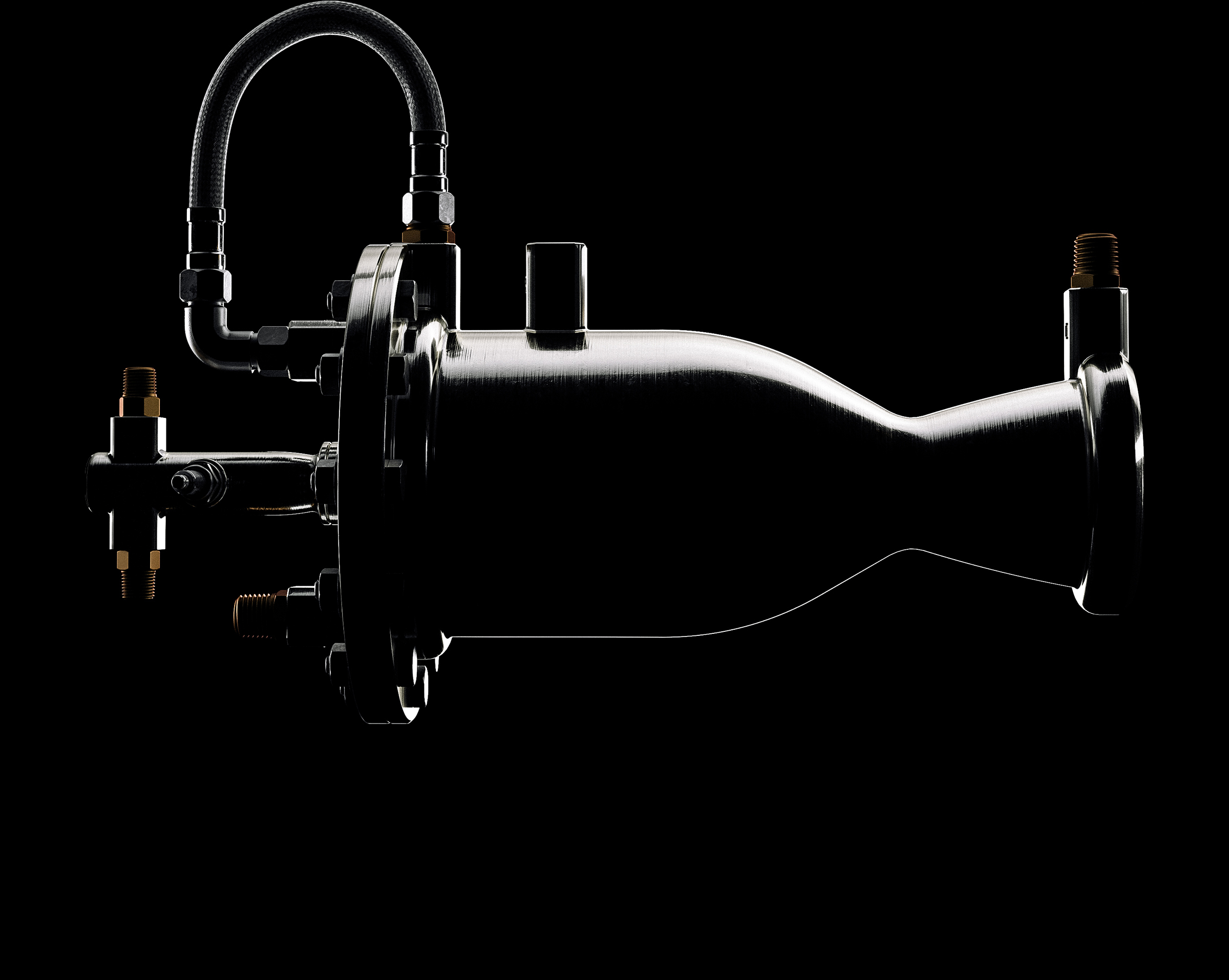
Launcher is a company that manufactures engines for space missiles using 3D metal printing. In recent years, Launcher has been on a research campaign to develop missile components in metal printing. The creation of the missile engines is the most complex stage in its development, the printing of the engines in 3D allows for the convenient and efficient creation of the missile engine without the need for welds and assemblies. In addition the metal printing allows for rapid and upgraded development, creating a complex geometry for the missile engine along with reducing costs and reducing the weight of the part. These characteristics are among the most important in the field of aerospace industry and in the field of space missiles in particular. The reduction in the weight of the parts made possible by the use of a metal printer, receives special emphasis when it comes to the field of the aerospace industry where every gram is important. Metal printers are finding their way into a variety of manufacturing industries. Today they are a significant competitive strength in the market and are the ones that enable the creation of groundbreaking products. But this is just the beginning! The technology is already here and now it is in our hands. The real revolution lies in what has been done with this technology. The metal printers open the door to a new world of industrial production that will surely later affect every product development method we know today.
- Chapter 1
What is 3D printing and what are its origins? - Chapter 2
The uses and purposes of 3D printing - Chapter 3
3D Printing Process - Chapter 4
How to choose 3D printing technology - Chapter 5
Overview of various 3D printing technologies - Chapter 6
General design guidelines for 3D printing - Chapter 7
CAD software classification - Chapter 8
3D Printing STL files: Introduction - Chapter 9
Understand common STL files errors and how to fix them - Chapter 10
SLS to MJF comparison - Chapter 11
Metal 3D Printing: Introduction - Chapter 12
How 3d metal printing change the world - Chapter 13
Metal 3D Printing Pros & Cons
- Chapter 1
What is 3D printing and what are its origins? - Chapter 2
The uses and purposes of 3D printing - Chapter 3
3D Printing Process - Chapter 4
How to choose 3D printing technology - Chapter 5
Overview of various 3D printing technologies - Chapter 6
General design guidelines for 3D printing - Chapter 7
CAD software classification - Chapter 8
3D Printing STL files: Introduction - Chapter 9
Understand common STL files errors and how to fix them - Chapter 10
SLS to MJF comparison - Chapter 11
Metal 3D Printing: Introduction - Chapter 12
How 3d metal printing change the world - Chapter 13
Metal 3D Printing Pros & Cons